All about Brushless motors - FAULHABER
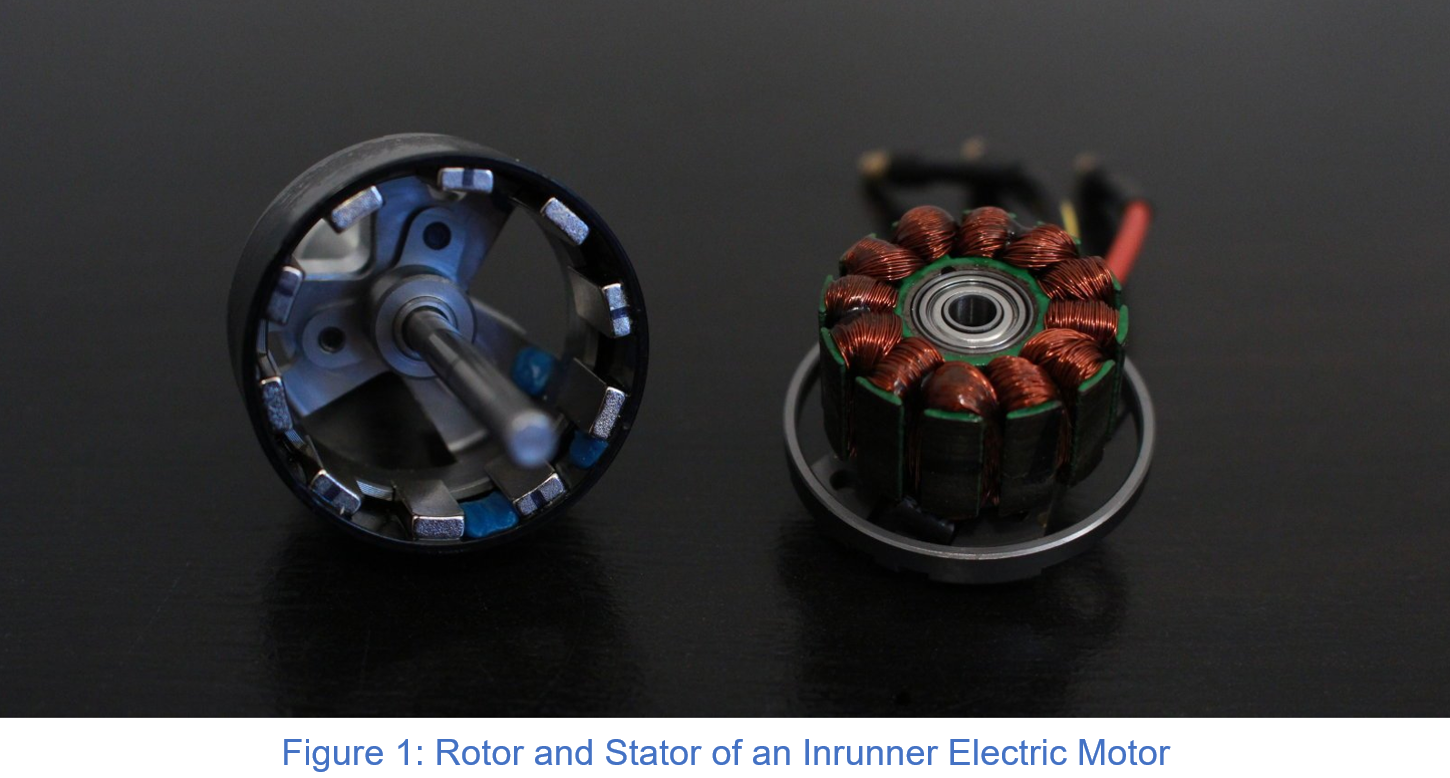
NEO 550 Brushless Motor - REV Robotics
Some Ideas on Selecting Dc Brush and Brushless Motors - Machine Design You Need To Know
When converting electricity into mechanical power, brushless motors are more effective than brushed motors primarily due to the lack of brushes, which minimizes power loss due to friction. The improved effectiveness is greatest in the no-load and low-load regions of the motor's performance curve. Environments and requirements in which producers use brushless-type DC motors include maintenance-free operation, high speeds, and operation where triggering is hazardous (i.

explosive environments) or might affect electronically sensitive equipment. The building and construction of a brushless motor looks like a stepper motor, but the motors have essential distinctions due to differences in application and operation. While stepper motors are often stopped with the rotor in a specified angular position, a brushless motor is normally planned to produce continuous rotation.

Amazon.com: DYS D2830 1300KV Brushless Motor for Multicopters RC Plane Helicopter: Toys & Games
Both a stepper motor and a properly designed brushless motor can hold limited torque at absolutely no RPM. Controller executions [modify] Because the controller carries out the traditional brushes' functionality it requires to understand the rotor's orientation relative to the stator coils. This is automatic in a brushed motor due to the fixed geometry of the rotor shaft and brushes.
The Single Strategy To Use For Brushless Motor - Adamant Namiki Precision Jewel Co., Ltd.
Others measure the back-EMF in the undriven coils to presume the rotor position, getting rid of the need for separate Hall effect sensing units. ARC Systems Inc. are for that reason frequently called sensorless controllers. Controllers that notice rotor position based on back-EMF have extra obstacles in starting movement because no back-EMF is produced when the rotor is fixed.
This can trigger the motor to run backwards briefly, including a lot more intricacy to the startup series. Other sensorless controllers can measuring winding saturation caused by the position of the magnets to infer the rotor position. [] A normal controller includes three polarity-reversible outputs managed by a reasoning circuit.
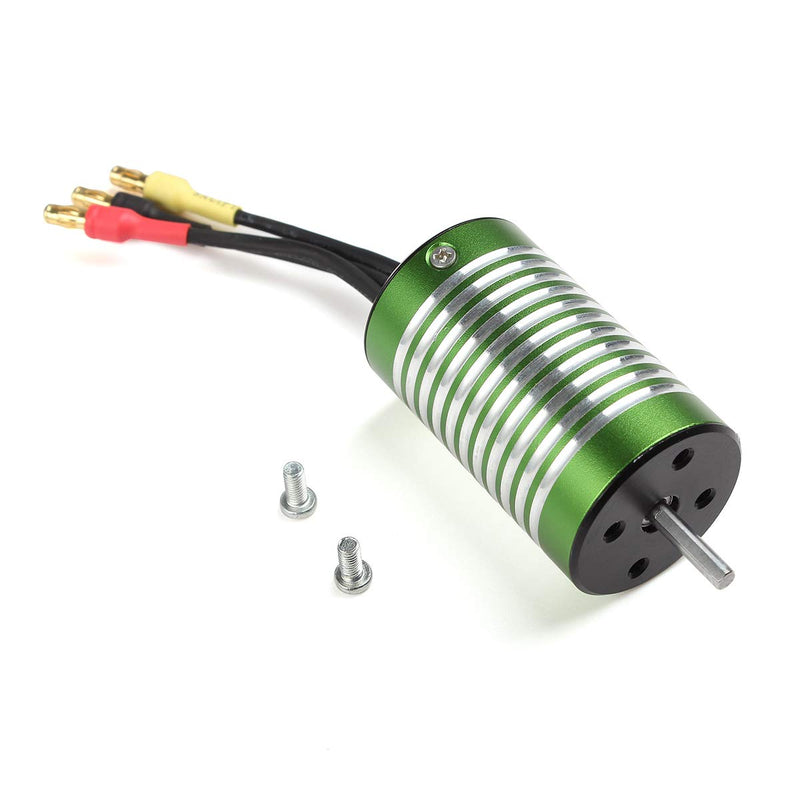
Brushless VsBrushed Motors - KDE Direct News Releases
More innovative controllers utilize a microcontroller to manage velocity, control motor speed and fine-tune performance. 2 key performance parameters of brushless DC motors are the motor constants K T \ displaystyle K _ T (torque constant) and K e \ displaystyle K _ e (back-EMF continuous, also called speed constant K V = 1 K e \ displaystyle K _ V = 1 \ over K _ e ).